Water Damage Series – Part 8: Safety
Worksite safety is our top priority. Even without the regulations and guidelines required by Occupational Safety and Health Administration (OSHA), Construemax (and every responsible mitigation company) is concerned with safety before anything else; the safety of the employees working in the space and anyone who may be in the work area. This means employing safety practices and using the appropriate Personal Protective Equipment (PPE).
When it comes to water damage situations there is a wide range of potential safety concerns. When your refrigerator water supply line bursts and floods your kitchen, the safety concerns might be slippery surfaces and that’s it. But a sewer backup, a tree that has fallen on the house during a storm, or the aftermath of a house fire, will all have many more things for the technicians to prepare for. Hurricanes can create some of the most dangerous situations.
Knowing the Risks
Before even coming to your home to help with water damage you, the property owner, will have spoken with someone at a mitigation company about the water intrusion. You will have let them know what is going on – what it is that has caused the water damage and what damage there is. From this conversation, the technician should not be walking into the situation completely ignorant. But top of their mind is knowing what risks there are.
Even before, and all throughout inspecting the water damage, they will be looking for potential problems. They will make visual observations, listen for problems, may touch affected areas, and use their sense of smell to detect potential hazards and assess the situation. You should expect them to draw the line at tasting anything though. Here is a shortlist of issues that your technician would be watching out for.
- Unsanitary water, like from a sewer backup, water intrusion from the outside, or water mixing with chemicals
- Odors such as gas leaks, chemicals, smoke, mildew, etc.
- Downed power lines or wet electrical boxes
- Structural damage, especially ceilings or walls that have fallen, or look like they might
- The presence of hazardous materials, this could be in water or in the building materials (like lead and asbestos) and it could be in storage containers, things like gasoline, pesticides, or household cleaners
- Pests, i.e. critters and bugs
The list of potential dangers is endless. With this initial assessment, the technician will proceed with the appropriate protective gear.
Personal Protective Equipment (PPE)
With recent events, we have all heard the term PPE used in relation to limiting the spread of COVID-19. Most would identify gloves and masks as PPE. And well they should. But PPE includes so many more things. Here is a list of items that are considered PPE:
- Gloves (work gloves, rubber gloves, chemical resistant gloves)
- Eye protection
- Respirators
- Protective clothing
- Hard hat
- Appropriate footwear
This is just a short list, as each of these categories includes different varieties of protective equipment.
Before the technician selects the appropriate PPE, he will try to eliminate the hazard. If that isn’t possible, he will employ methods or practices that will diminish the risk. And the last level of protection is his personal protective equipment.
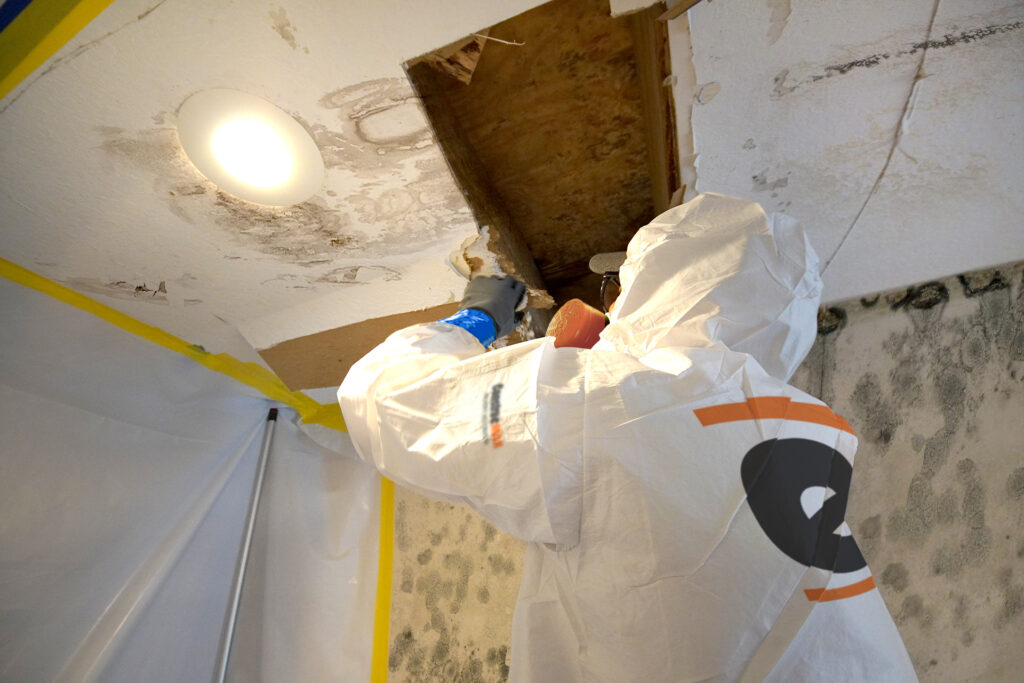
PPE is the Last Level of Protection
This might seem backward. Rather than last, it might seem to be the first level of protection, but not so. The first level of protection or safety is the elimination of the hazard. It’s like a trick question. It’s obvious when you see it.
Eliminate: Suppose there are exposed electrical wires near water (or anywhere on the property). The way to eliminate the hazard is to cut power to the house.
Work Practices: When heavy or bulky items need to be moved, the team can carry the items together rather than one person struggling alone.
PPE: A sewer backup can’t be eliminated before the tech goes to work because that IS his work. He must use rubber boots, gloves, face coverings, protective eyewear, etc. to protect himself.
Even after cutting power, the tech will still be careful working around the wires, perhaps by wearing electrician’s gloves, their PPE. The team carrying heavy items will still rely on back braces as PPE to limit the risk of injury. The PPE is the last line of protection after everything else has been considered.
PPE for the Occupants of the Property
If the worksite is genuinely dangerous, requiring the water technician to wear PPE, that risk should be considered by anyone who remains inside the property for their safety as well. This falls into the category of eliminating the threat, that’s what the mitigation team is there for.
In an example above I referenced a refrigerator line that floods the kitchen. This would clearly not require you to move out of your home until the place is dry (because this is a hypothetical, there are no extenuating circumstances that would suggest anything else). But just as the technician would be very careful about slips and falls on the wet surface, you too would need to be careful.
If the situation were a sewer backup, or a significant mold infestation as a result of the water loss, and the technician is unable to enter the property without a respirator, then it would be inadvisable for anyone else to enter the property without a respirator either.
Temporary Barriers are Common
It can’t be said too many times that every water loss situation is unique. You may have a technician inspect your water damage, place a few pieces of equipment, and a few days later everything is back to normal. But things are usually a bit more involved than that.
One of the key components of a water loss mitigation strategy is containment. Preventing the spread of water is key, of course, but airborne contaminants as well.
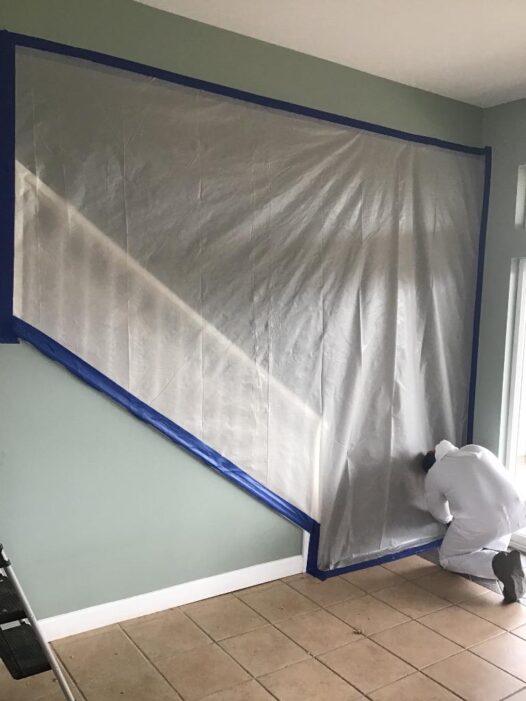
For example, with water and time comes microbial growth. Microbial growth can lead to full on mold. The effects of mold can range from making people merely uncomfortable – to very sick; in severe cases, it can cause death. Like mold, smoke has very fine particles and those particles can get into tiny cracks and crevices.
A plastic barrier will often be used to contain the affected area. Plastic may be placed over ventilation ducts, between rooms or to a section of a room. Often there will be zippers in the middle to allow you to pass through so the space can still be accessed but prevent extended exposure of a contaminated area into an uncontaminated area.
These containment measures serve two purposes, one is to prevent additional damage throughout the property, but the other is simply safety.
Microbial Growth vs. Mold
Quite often you will hear (or read) about microbial growth rather than it being referred to as mold. The primary reason for that is that mold is a specific type of microbe. Not all microbes are mold. Mold is very common, especially here in Florida where there is such a high humidity year round. Bacteria is also a microbe that grows in colonies and can reach a size that would be visible to the naked eye. Neither is a welcome guest.
When a water mitigation technician is in your home and discovers microbial growth, he doesn’t know if it is mold. If he were to place bets on it being mold each time he spots it, he would win a lot of bets. But there are no bookmakers for that.
To give you the best service, and to follow the law, when the amount of microbial growth is greater than 10 square feet of surface area, an expert must be called in to evaluate it.
Environmental Experts
The water mitigation team will call in an expert to evaluate the microbial growth that is discovered. These experts might be called Industrial Hygienists or Indoor Environmental Professionals, but they are trained specifically for this purpose, to determine the fitness of indoor spaces for people to be able to live or work safely.
They will look to see where the infestation is – and where it has spread. They will provide the mitigation team with a protocol for mitigating the infestation.
The term protocol, in this context, is going to be a guide of instructions. It will specify what materials must be removed, what areas must be cleaned, and what methods are acceptable for cleaning. Sure, that makes sense, because that’s what protocol generally means, a set of instructions. But unlike computer science or diplomatic protocols, the fate of the world doesn’t hinge on it. So the approach taken is left to the mitigation professional to determine.
Nevertheless, the Industrial Hygienist’s concern is the safety of the property and the health of its occupants.
A Protocol Is Not an Insurance Approval
It must be very clearly understood that when an Industrial Hygienist writes up a protocol or a post mitigation clearance, they are writing a professional opinion about the safety of the property. This is a separate issue from insurance coverage, what insurance will cover and what they will not.
When an insurance policy has a rider for mold, there is going to be a limit. Most limits are $10,000 (higher limits are usually available for a higher premium). The cost of the mold mitigation can very easily exceed that limit. The Industrial Hygienist doesn’t have access to your insurance policy, they don’t know what limits you have, what exclusions you have, and they are not licensed to determine for your insurance company if something will or will not be covered. They might not even be aware of whether or not there is even insurance on the property.
To repeat, the Industrial Hygienist’s concern is the safety of the property and the health of its occupants. As such, in the protocol, they write what is needed to make the area safe.
Whether the insurance company covers that cost or not is not their concern in doing their evaluation. But it is something you would have to discuss with your adjuster.
A Structural Engineer May Be Needed for Safety
An Industrial Hygienist is not the only expert that might be needed to evaluate safety. There may be times when there are structural concerns. Suppose a tree falls on a house, or a car drives through the side of a building, either of these could cause structural damage that would threaten the safety of anyone or anything inside.
If there is any doubt about the structural integrity of the work area, a Structural Engineer may be called upon to give guidance. This very often will happen after the mitigation is complete as a precursor to the build-back of the property, but if a worksite is not safe because of a risk of collapse, the technicians will not enter without first getting an ‘all clear’ from a Structural Engineer.
Summary
Safety is the most important part of all we do in water mitigation. Everyone’s safety, not just the technicians, but the occupants of the property as well.
The PPE, the containment, and expert evaluations have come about from years of experience. Safety is the sole purpose of OSHA and they provide not only guidance for the industry, they provide mandates which all mitigation companies are obligated to follow.
The mitigation and restoration industry has also created standards. They have done so with three things in mind, safety, preservation or salvage of property, and restoration where salvage isn’t possible. The first is always safety.
Our technicians are the beneficiaries of the industry experience and the OSHA regulations, and ultimately, you are beneficiaries of these safety measures as well.